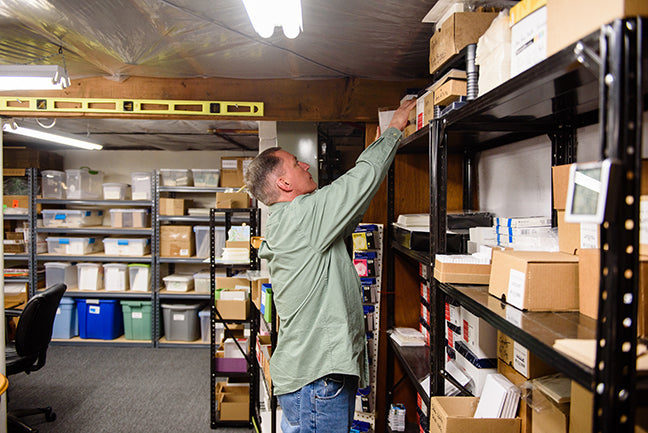
People who have visited our workshop are very quick to comment “Wow, it is so organized.” I will admit I have a sense of pride when I hear those words. Sometimes when working in a large shop with many people around, it is harder to keep things in order. I have the advantage of working in this area on my own, so if it becomes chaotic, I have no one to blame but myself.
When working with a lot of different products, raw material, packaging, finished products and shipping materials, I try to keep similar products together. Although some products may be used in more than one area.
I try to think about the process of what I am trying to make. I try to envision a start to finish order of operation. I know that sometimes in business, it is more important to get going and get the work done, just to stay in business. I find that even when I am working, my mind will still be searching for a better, or easier way to do the job.
I did not set up my area perfectly on the first time, sometimes it is just trying to find a place for everything and not to block the pathways and keep the area safe. It is more important to be safe, even if it means a few more steps to finish a work order.
If you had an unlimited amount of space, this exercise in organizing would be so easy. However most small businesses, like ours, are limited in actual square feet so I have had to think and rethink to find and use all the available space. I put free standing shelves, 34’’wide x 16’’ deep, 4 shelves high, along a wall and created a hallway type of passage between two work areas, it worked out well for a while. Then I took some measurements and realized I could use a wider storage shelf, 48’’wide x 24’’deep, 5 shelves high, and I still have plenty of room to pass through and I increased my storage space by over 60%.
I found that solution and then reexamined my entire space. I removed some cabinets that I thought were a good storage solution and found that a large shelving unit created twice the storage and a flat work space. Another solution for paper products (raw material) was to purchase 2 shelf units, with 4 shelves per unit, and combine the shelves onto one unit, for a total of 8 shelves. With paper it is easier to separate the different products than to stack them and dig through a pile. There are also several products used for kitchen cabinets that create a shelf inside a shelf, great for separating same size paper products by color or weight.
In the beginning it was a question of cost, so I did choose some of the cheaper options. But when I consider all the space that was made available through the purchase of the larger shelves, I no longer question the decision to upgrade and spend the money. If you are truly limited to an area, make the most out of every square foot.
With more space available, I try to put similar products together. I group my start products together, envelopes, papers, and inks. I try to place these items as close to the actual production area (equipment) as possible. I think about what happens after production, what other work needs to take place before this becomes a finished product. I designate an area where the half-completed products will not get damaged while I continue with other tasks. When production is completed, I make room for the products to be packaged, some products will be packaged for immediate shipping and others will be packaged and stored with existing inventory.
Shipping supplies take up room, so I keep them as far as possible from the production area. Storage of finished products and some randomly used raw material are kept further away.
For most, these tasks will take place in a single area, so I find it best to not over stress the area. When I finish a part of the process, I clean up the area and put material and tools back in their place. Sometimes I will have multiple jobs taking place at one time, I do not use this as an excuse for clogging up the area or damaging other products. I must become creative with the space, I may use a folding table for layout or storage. I may also have to take equipment off a flat surface and store it under a table.
This may seem frustrating and time consuming, and sometimes it is. What is even worse is ruining a finished product in the last stage of production by being lazy about keeping the area organized. Our products are paper and very fragile, a bent corner can ruin the presentation, and people are counting on us to be mindful. If my area is cluttered, I feel like my mind is cluttered, if my area is organized, maybe the mind will follow.
Thanks for checking in with us at El’s Cards.
And thank you Melissa Mullen Photography for the wonderful photos of Bob's workshop.